The Best Machine Condition Monitoring Tools and Technologies
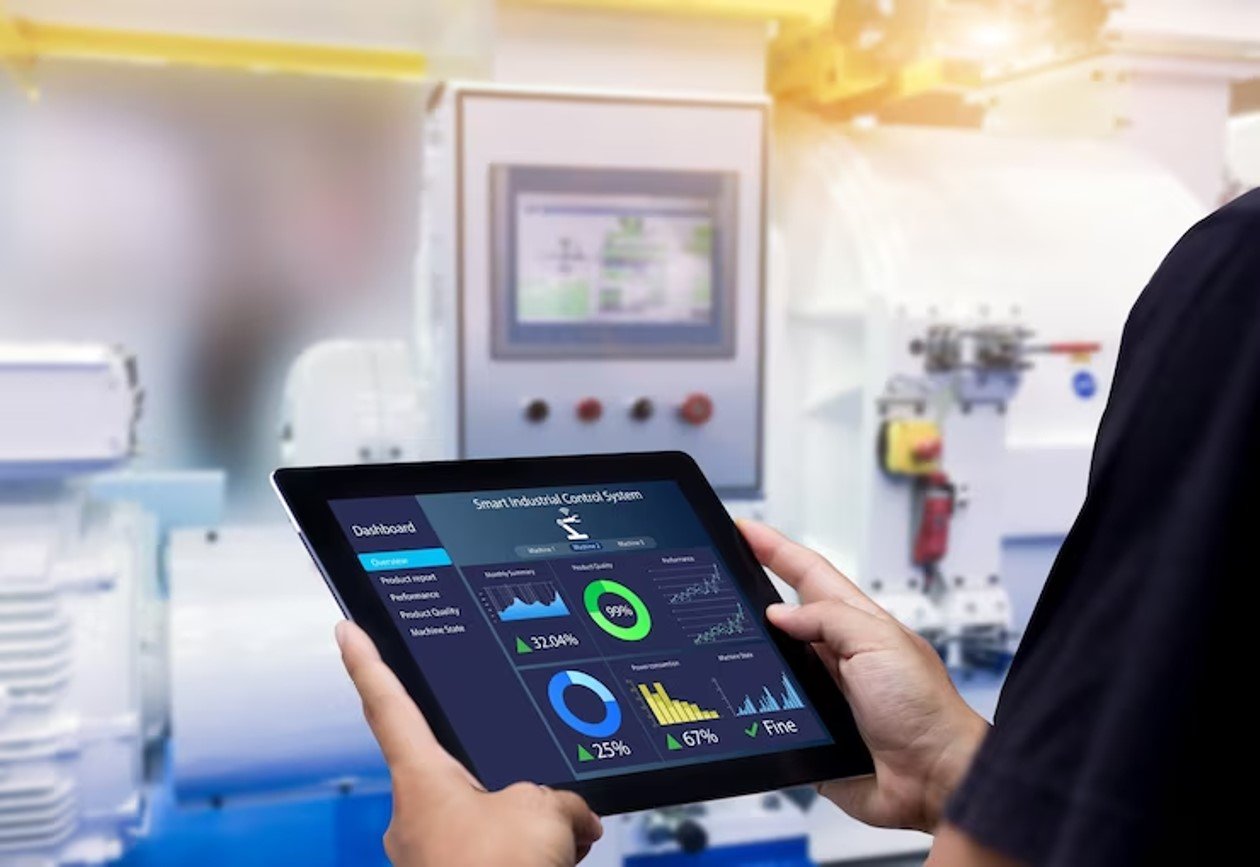
In today’s industrial landscape, the efficient functioning of machinery is critical to productivity and profitability. Any unexpected machinery failure can result in costly downtime and repairs. This is where Machine Condition Monitoring (MCM) tools and technologies come into play. MCM provides real-time insights into the health of industrial equipment, enabling proactive maintenance, reducing downtime, and extending the lifespan of machinery.
Importance of Machine Condition Monitoring
MCM is essential because it allows companies to move from a reactive maintenance model to a proactive one. Instead of waiting for a breakdown, businesses can monitor their machinery continuously. This shift in approach offers several advantages, including increased efficiency, reduced maintenance costs, and improved workplace safety.
Types of Machine Condition Monitoring Tools
Vibration Analysis
Vibration analysis is a widely used MCM technique. It involves measuring the vibration levels of machinery to detect abnormalities. These abnormalities can indicate misalignments, unbalanced components, or worn-out bearings.
Infrared Thermography
Infrared thermography uses thermal imaging to identify temperature variations in machinery. It’s particularly effective for electrical systems and can detect loose connections or overheating components.
Ultrasonic Testing
Ultrasonic testing listens to the high-frequency sound waves emitted by machinery. Irregular sounds may indicate issues like leaks, friction, or cavitation.
Oil Analysis
Oil analysis examines the condition of lubricating oils. It can identify contaminants, wear particles, and oil degradation, providing insights into the condition of the machinery’s moving parts.
Acoustic Emission
Acoustic emission monitors stress waves generated by machinery. This method is useful for detecting cracks and faults in materials, making it valuable for industries like aerospace and manufacturing.
Read More: The Role of Machine Learning in Predictive Analytics 2023
Emerging Technologies
IoT and Machine Learning
The integration of the Internet of Things (IoT) and machine learning has revolutionized MCM. IoT sensors collect data in real time, and machine learning algorithms analyze this data to predict when maintenance is required accurately.
Wireless Sensor Networks
Wireless sensor networks have eliminated the need for complex wiring. They provide real-time data, making monitoring more accessible and cost-effective.
Augmented Reality (AR)
AR has found applications in MCM by providing technicians with real-time information and virtual overlays for repair guidance.
Benefits of Machine Condition Monitoring
- Increased machinery uptime
- Cost-effective maintenance
- Enhanced safety for personnel
- Prolonged machinery lifespan
- Improved overall productivity
Challenges and Considerations
Implementing Machine Condition Monitoring (MCM) presents several challenges and considerations for businesses. While the benefits are substantial, it’s important to address these hurdles to ensure a successful MCM strategy.
Investment and Training
One of the primary challenges is the initial investment required for MCM tools and technologies. This includes the purchase of monitoring equipment, sensors, and data analysis software. Additionally, companies must allocate resources for employee training to effectively operate and interpret data from these systems.
Data Analysis Capabilities
Collecting data is one thing, but analyzing it effectively is another challenge. Companies must develop or acquire the capability to process the vast amount of data generated by MCM systems. With proper data analysis, the valuable insights these systems offer can be harnessed.
Data Security and Privacy
With the increasing reliance on data-driven technologies, data security and privacy have become significant concerns. Protecting the data collected from machinery is crucial. Companies need to establish robust cybersecurity measures and ensure compliance with data privacy regulations to prevent unauthorized access and data breaches.
Integration with Existing Systems
Integrating MCM systems with existing machinery and information technology infrastructure can be complex. Compatibility issues may arise, and it’s essential to ensure that data from MCM tools can be seamlessly incorporated into the organization’s maintenance and operational processes.
Maintenance Scheduling
MCM may lead to a shift from reactive maintenance to predictive or preventive maintenance. This transition requires careful planning and scheduling to minimize downtime and disruptions in production.
Overcoming Resistance to Change
Employees may be resistant to new technologies and processes. To successfully implement MCM, companies must invest in change management strategies and ensure that their staff is comfortable with and receptive to these changes.
Scalability
As businesses grow, their machinery and operational complexity may increase. MCM systems must be scalable to accommodate this growth. Companies should choose solutions that can expand their needs.
Return on Investment (ROI)
Calculating the ROI of MCM can be challenging, as it involves both tangible and intangible benefits. Companies need to assess the long-term gains in terms of reduced maintenance costs, increased efficiency, and extended equipment lifespan.
In conclusion, while implementing Machine Condition Monitoring offers substantial benefits, businesses must address these challenges and considerations to reap the rewards effectively. With proper planning, investment, and a commitment to data security, MCM can transform maintenance practices, enhance operational efficiency, and contribute to long-term success.
Implementation and Best Practices
Successful MCM implementation involves choosing the right tools, setting up a robust data analysis system, and training staff. Best practices include regular data collection, analysis, and using the insights for preventive maintenance.
Real-world Case Studies
Let’s explore two real-world examples of MCM success stories:
- A manufacturing plant reduced breakdowns by 60% and maintenance costs by 40% by implementing vibration analysis.
- An energy company improved equipment reliability and cut downtime by 30% using IoT sensors and machine learning.
Future Trends
Machine Condition Monitoring (MCM) is a dynamic field that continues to evolve with advancements in technology. Several exciting trends are shaping the future of MCM, providing new opportunities for businesses seeking to stay competitive in the industrial landscape.
Artificial Intelligence (AI) Integration
Machine Condition Monitoring: The integration of Artificial Intelligence is a game-changer in MCM. AI algorithms can analyze vast amounts of data from sensors and predict potential machinery issues with remarkable accuracy. Machine learning models can adapt and improve over time, providing even more precise insights into the health of equipment.
5G Connectivity
The rollout of 5G networks is set to revolutionize MCM. High-speed, low-latency connections will enable real-time data transfer from machinery to monitoring systems. This will allow for quicker response times and more immediate actions in case of abnormalities.
Edge Computing
Edge computing involves processing data locally on the machinery or on nearby servers rather than sending it to a central data center. This trend reduces latency and enhances real-time monitoring capabilities, making it particularly beneficial for critical industrial processes.
Remote Monitoring
Advances in Connectivity and cloud technology enable remote monitoring of machinery from anywhere in the world. Technicians can access real-time data, perform diagnostics, and make informed decisions without being physically present, reducing response times and travel costs.
Predictive Analytics
Predictive analytics will continue to grow in importance. By analyzing historical data and real-time sensor data, MCM systems can predict when maintenance is required with even greater accuracy. This minimizes downtime and maximizes machinery lifespan.
Condition-Based Spare Parts Inventory
MCM will facilitate the development of condition-based spare parts inventory systems. By accurately predicting which components are likely to fail, companies can stock only the necessary spare parts, reducing storage costs and waste.
Sustainability and Energy Efficiency
Machine Condition Monitoring: The focus on sustainability and energy efficiency is driving MCM to contribute to reducing energy consumption and environmental impact. Monitoring systems can detect inefficiencies and recommend adjustments to reduce energy usage and lower carbon footprints.
Human-Machine Collaboration
Machine Condition Monitoring: Collaboration between humans and machines will become more pronounced. Augmented Reality (AR) and Virtual Reality (VR) technologies will assist technicians in maintenance tasks, providing real-time guidance and overlays of equipment diagnostics.
Read More: Why Data Analytics is Essential for Digital Marketing Success
Conclusion
Machine Condition Monitoring tools and technologies are transforming the industrial landscape. They offer proactive maintenance, cost savings, and enhanced safety. As technology continues to advance, MCM will only become more crucial for businesses seeking to stay competitive in today’s fast-paced world.
FAQs
What is Machine Condition Monitoring?
Machine Condition Monitoring is a process that involves the use of various tools and technologies to track the health and performance of industrial machinery to predict and prevent failures.
How does Vibration Analysis work?
Vibration analysis measures the vibration levels of machinery. Irregular vibrations can indicate problems such as misalignments or worn-out components.
What are the benefits of implementing Machine Condition Monitoring?
Implementing MCM leads to increased machinery uptime, reduced maintenance costs, improved safety, prolonged machinery lifespan, and enhanced overall productivity.
Are there any challenges in implementing MCM?
Yes, challenges include the need for training, technology investment, data analysis, and data security considerations.
What are the future trends in Machine Condition Monitoring?
The future of MCM is marked by advancements in AI, 5G, and edge computing, enabling more precise and real-time monitoring. This will further reduce costs and enhance efficiency.